High precision linear tables
Features
High precision linear tables LTP and LTPG are particularly suitable, due to their construction and high guidance accuracy, for the precise positioning of moderate and high loads. These tables are supplied assembled.
Aluminium design
High precision linear tables LTP
High precision linear tables LTP comprise:
- a base plate made from aluminium
- two high precision two-row linear recirculating ball bearing and guideway assemblies KUE or, by agreement, two four-row linear recirculating ball bearing and guideway assemblies KUVE in the case of LTP15 or two six-row linear recirculating ball bearing and guideway assemblies KUSE in the case of LTP25 with two carriages per side. The linear recirculating ball bearing and guideway assemblies are preloaded clearance-free and run without stick-slip
- a carriage unit made from aluminium with a central lubrication system for relubricating the carriages of the linear recirculating ball bearing and guideway assemblies and the spindle nuts
- a rolled ball screw spindle with a single flanged nut F. In the case of some pitch values, double flanged nuts FM are possible. A double nut FM comprises a single flanged nut paired with a cylindrical single nut. Double nuts are preloaded
- a locating bearing housing made from aluminium alloy with a preloaded double row angular contact ball bearing ZKLF and a lubrication nipple
- a non-locating bearing housing made from aluminium alloy with a needle roller bearing NA and a lubrication nipple.
The spindle support bearings, carriages and spindle nuts have an initial greasing, are sealed and can be relubricated.
Cast iron design
High precision linear tables LTPG
High precision linear tables LTPG comprise a base plate, a carriage unit and a bearing housing made from cast iron. They are suitable for applications requiring increased accuracy and have good vibration behaviour. High precision linear tables LTPG differ from linear tables LTP in that they have:
- a base plate made from cast iron with ground seating and locating surfaces for the guideways
- two high precision six-row linear ball bearing and guideway assemblies KUSE with two carriages per side
- a carriage unit made from cast iron with a ground surface and seating surfaces for the carriages
- a locating bearing housing made from cast iron
- a non-locating bearing housing made from cast iron.
With bellows
High precision linear tables LTP and LTPG can be equipped with two sets of bellows.
The bellows are attached by means of screws.
For the same stroke length, the total length of a linear table with bellows is greater than the total length of a linear table without bellows.
Screw drive
The spindle thread has a pitch value of between 5 mm and 50 mm, see table. As standard, single flanged nuts with an axial clearance dependent on the pitch are used. In the case of some pitch values, the ball screw drive can be supplied with preloaded double nuts.
Screw drive variants
Screw drive variants | Suffix | ||
---|---|---|---|
Pitch | 5 | mm | 5 |
10 | mm | 10 | |
20 | mm | 20 | |
40 | mm | 40 | |
50 | mm | 50 |
Drive elements
The information on drive elements in high precision linear tables LTP and LTPG matches the information on drive elements in linear tables LTE.
Special designs
Special designs of high precision linear tables, including the following, are available by agreement:
- with a rolled or ground ball screw spindle with an accuracy of 25 μm/300 mm
- with anti-corrosion coating of the spindle and/or linear recirculating ball bearing and guideway assemblies
- with special bellows, for example in a version resistant to welding beads
- with a trapezoidal screw drive
- with special hole patterns on the carriage unit and base plate in accordance with customer requirements.
Design and safety guidelines
The design and safety guidelines for high precision linear tables LTP and LTPG essentially match the design and safety guidelines for linear tables LTE. The following pages describe exclusively the differences between the high precision linear tables LTP and LTPG and the linear tables LTE.
Deflection
High precision linear tables LTP and LTPG are essentially dependent on the adjacent construction. It is not therefore possible to provide data or diagrams for the deflection.
Length calculation
of linear tables
The length calculation of linear tables is based on the required effective stroke length NH. The effective stroke length NH must be increased by the addition of safety spacing values on both sides of the travel distance. It is only if bellows are present that the effective length BL must be added.
The total length Ltot of the linear table is determined from the total stroke length GH, the lengths of the end plates L4 and L5 on both sides and the carriage plate length L.
Parameters for length calculation
GH | mm | Total stroke length |
NH | mm | Effective stroke length |
S | mm | Safety spacing, see table |
L | mm | Total length of carriage unit |
L2 | mm | Length of base plate |
L4 | mm | Length of end plate |
L5 | mm | Length of end plate |
Ltot | mm | Total length of linear table |
BB | mm | Length of bellows fastener |
BL | mm | Effective length of bellows |
FBL | Effective length factor according to linear table type. |
Total stroke length GH
The total stroke length GH is determined from the required effective stroke length NH and the safety spacings S, which must correspond to at least the spindle pitch P.
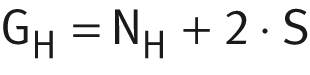
Maximum length of linear tables
The maximum length Ltot of high precision linear tables LTP and LTPG is 3 500 mm.
In the case of a total length Ltot < 2 · L + L4 + L5 + 30, not all fixing holes in the support rail will be accessible, so please consult us.
Total length Ltot
The following ➤ equtions are designed for one linear table. The parameters and their position can be found in ➤ Figure and the table.
Length parameters for one high precision linear table
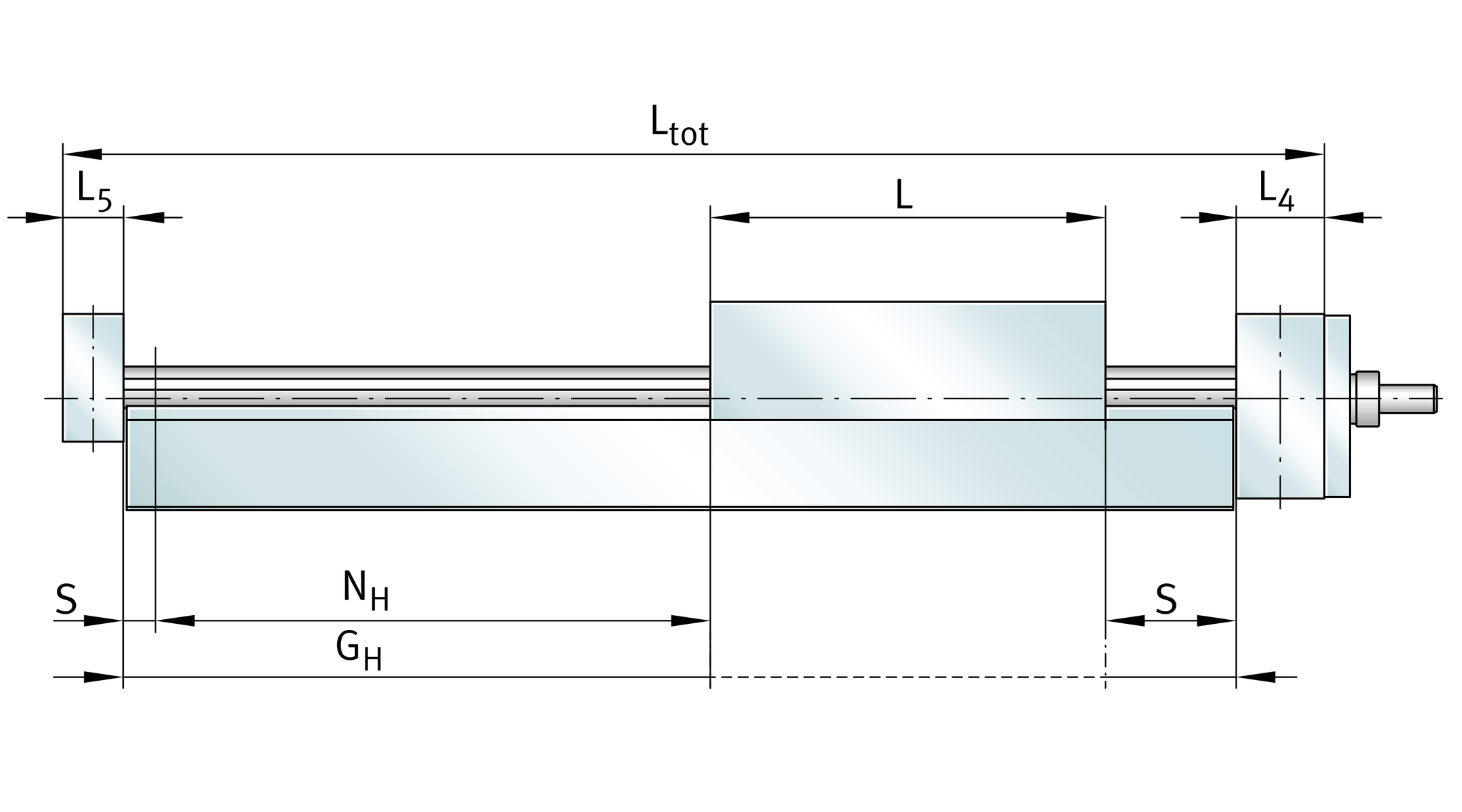
Linear table LTP without bellows

Linear table LTP with bellows

Length parameters
Designation | Spindle pitch P | L | L4 | L5 | S | FBL | BB |
---|---|---|---|---|---|---|---|
mm | mm | mm | mm | mm | mm | ||
LTP15-185 | 5 | 185 | 35 | 25 | 5 | 1,35 | 28 |
10 | 10 | ||||||
20 | 20 | ||||||
50 | 50 | ||||||
LTP15-275 | 5 | 275 | 35 | 25 | 5 | 1,35 | 20 |
10 | 10 | ||||||
20 | 20 | ||||||
50 | 50 | ||||||
LTP25-325 | 5 | 325 | 35 | 30 | 5 | 1,27 | 20 |
10 | 10 | ||||||
20 | 20 | ||||||
40 | 40 |
Effective length of bellows
The effective length of bellows is the length occupied by the bellows in the fully compressed state. Calculation is based on the total stroke length GH, ➤ Figure, ➤ equation and table.
Effective length calculation
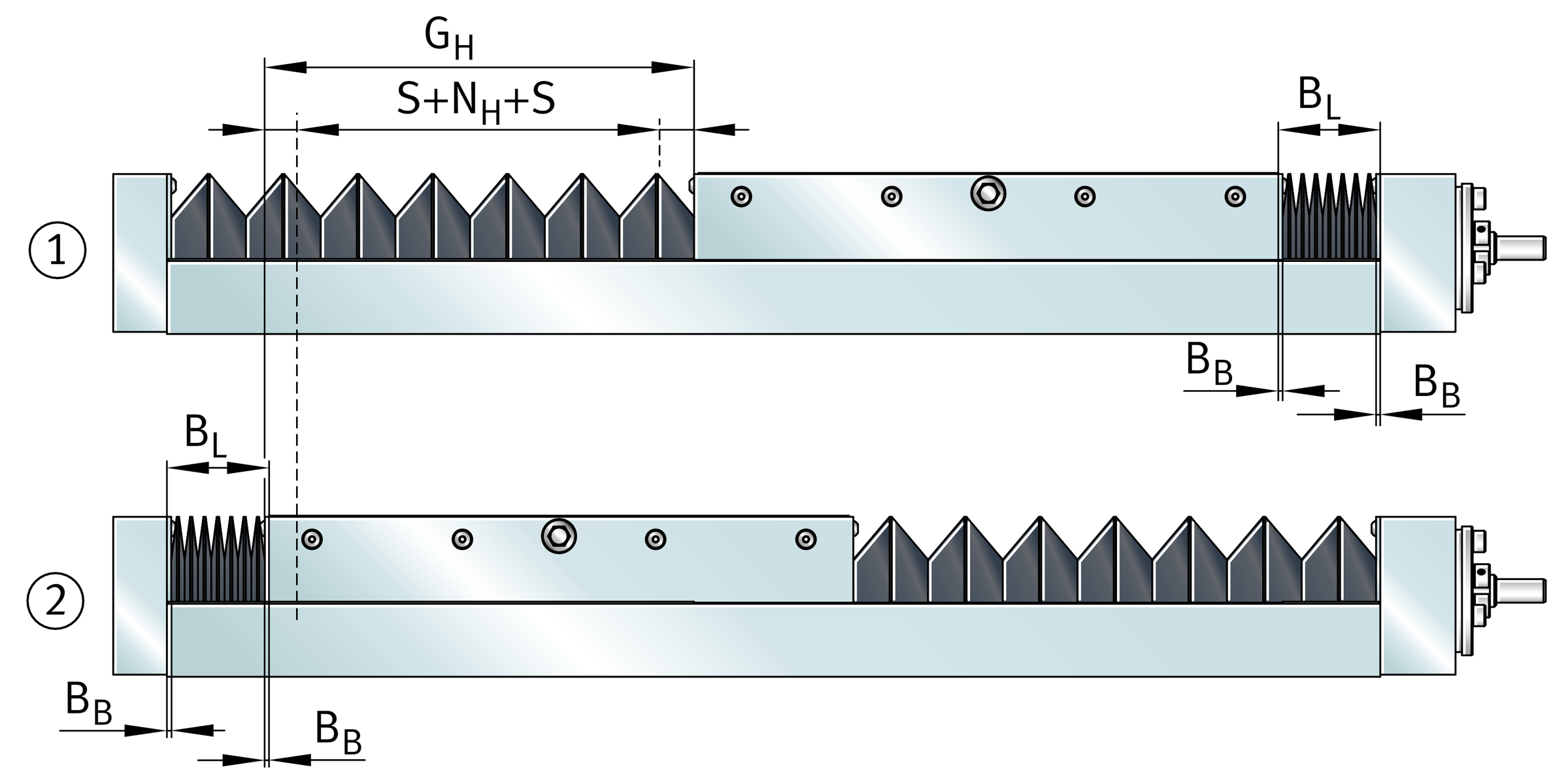


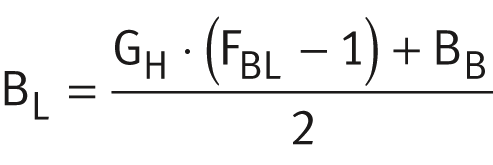
BL | mm | Effective length of bellows |
GH | mm | Total stroke length |
FBL | Effective length factor according to linear table type, see table | |
BB | mm | Length of bellows fastener. |
Calculation of hole pattern of base plates
Base plates are supplied as standard with a symmetrical hole pattern. If a symmetrical hole pattern is present: aR = aL. In the following calculation, the values must not be less than the value aR min (aL min).
Parameters for hole pattern calculation
aR, aL | mm | Left and right spacing between the end of the base plate and the nearest hole centre point, ➤ Figure and ➤ Figure |
jL8 | mm | Hole spacing |
L | mm | Total length of carriage plate |
L2 | mm | Total length of base plate |
L4, L5 | mm | Lengths of bearings |
Ltot | mm | Total length of linear table |
JB8 | mm | Hole spacing of inner row of holes |
JB9 | mm | Hole spacing of outer row of holes. |
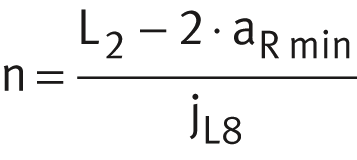

Spacings aR and aL on the base plate
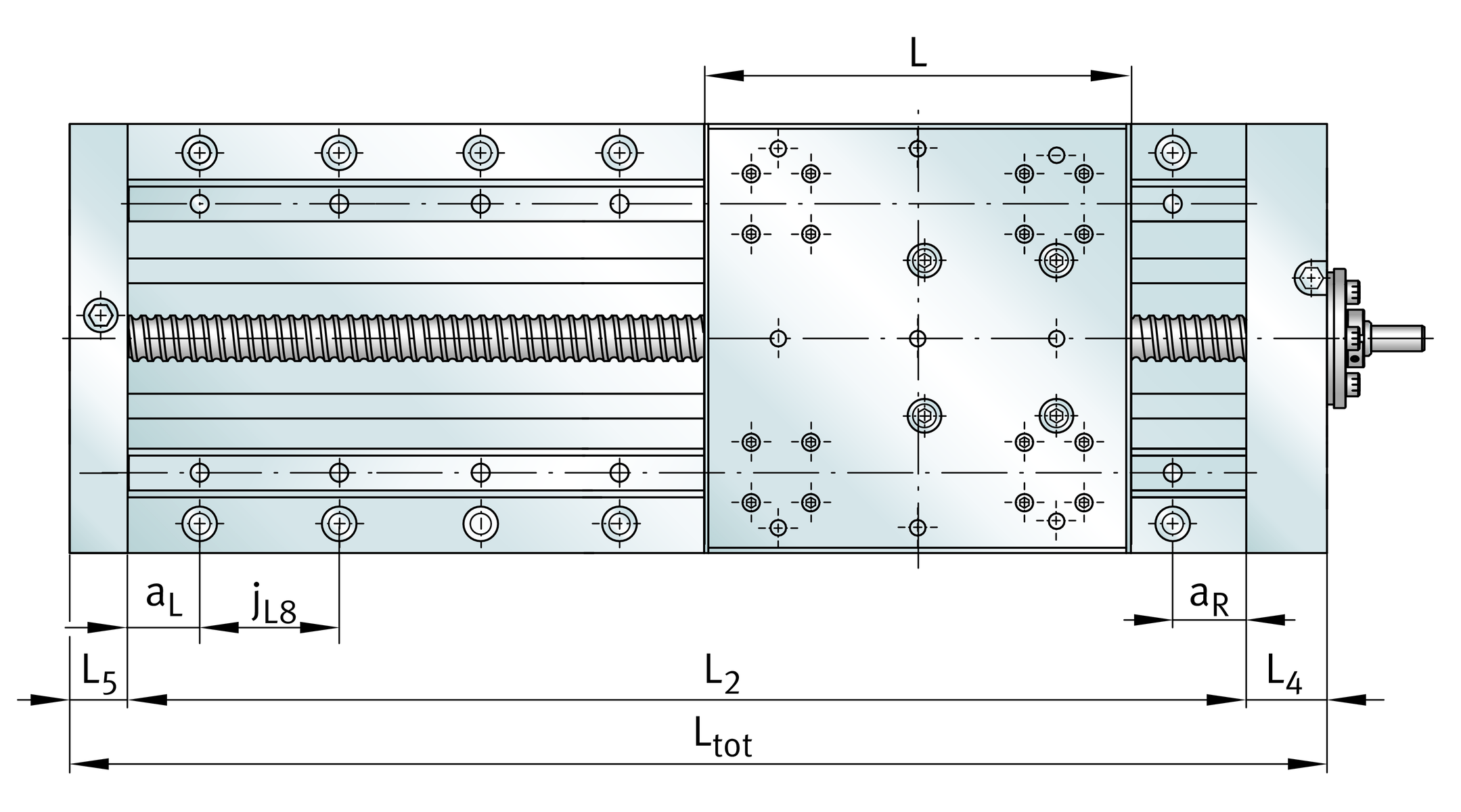
Spacings aR and aL on the base plate in double rows of fixing holes
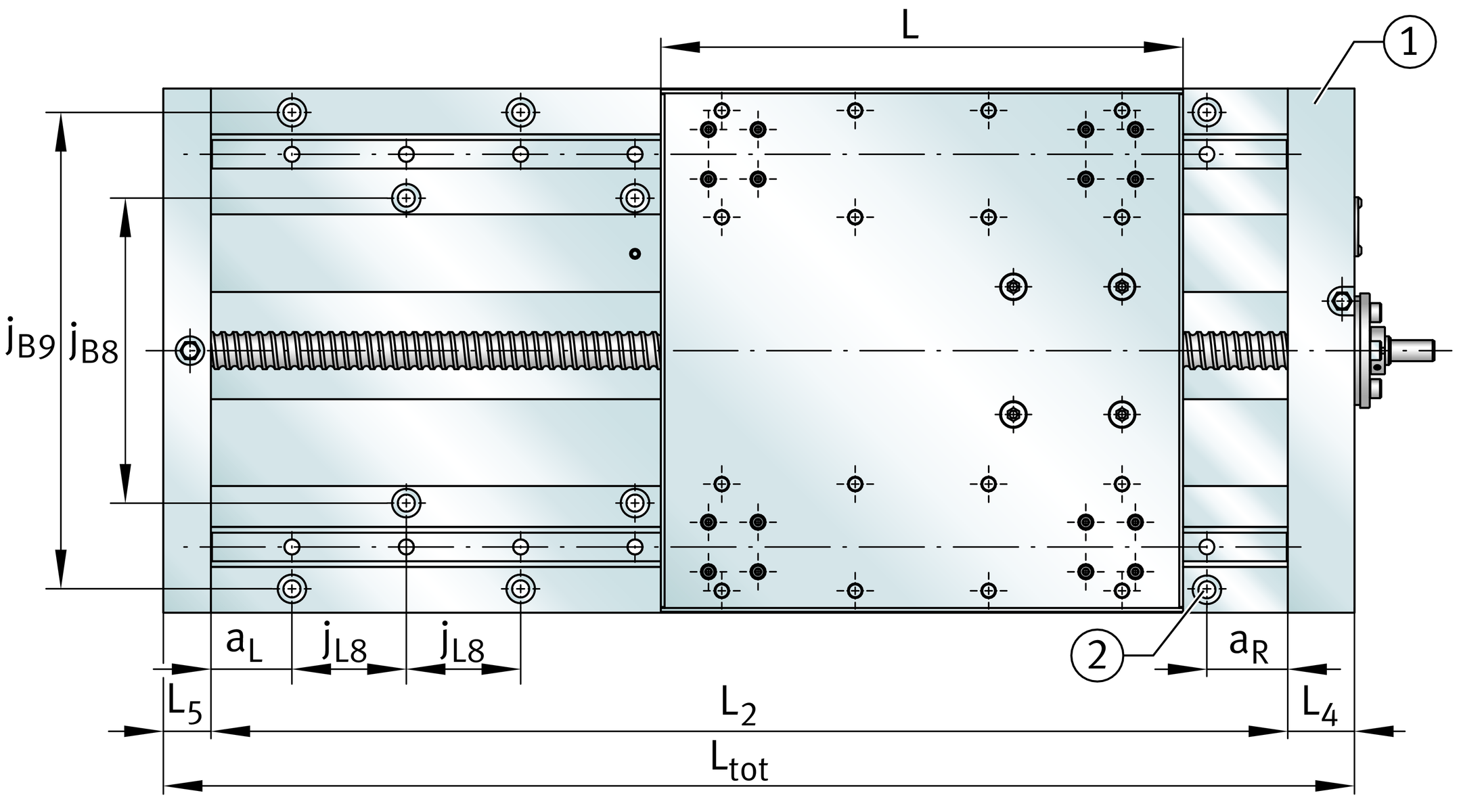


ATTENTION
In the case of a total length Ltot < 2 · L + L4 + L5 + 30, not all fixing holes in the base plate will be accessible, so please consult us.
ATTENTION
In the case of double rows of fixing holes, the first fixing hole is always in the outer row on the locating bearing side, ➤ Figure.
Mass calculation
The total mass of a linear table is calculated from the mass of the table without a carriage unit and the carriage unit.

Values for mass calculation, aluminium design
Designation | Mass | |
---|---|---|
Carriage unit** | Table without carriage unit | |
mLAW | mBOL | |
≈kg | ≈kg | |
LTP15-185 | 3,5 | (Ltot – 60) · 0,018 1 + 2,6 |
LTP15-275 | 6,4 | (Ltot – 60) · 0,025 8 + 3,6 |
LTP25-325 | 12,3 | (Ltot – 65) · 0,043 3 + 6,2 |
Values for mass calculation, cast iron design
Designation | Mass | |
---|---|---|
Carriage unit** | Table without carriage unit | |
mLAW | mBOL | |
≈kg | ≈kg | |
LTPG15-185 | 6,4 | (Ltot – 60) · 0,041 9 + 5,5 |
LTPG15-275 | 13,8 | (Ltot – 60) · 0,052 8 + 8,1 |
LTPG25-325 | 26,5 | (Ltot – 65) · 0,084 4 + 13,9 |
**Including single or preloaded double nut.
Lubrication
The information on the lubrication of LTP and LTPG substantially matches the information on the lubrication of LTE. The only differences are in the relubrication quantities and relubrication points.
Relubrication
Relubrication should be carried out wherever possible with several partial quantities at various times instead of the complete quantity at the time of the relubrication interval. Relubrication quantities, see table.
Relubrication quantity per lubrication nipple
Series | Carriage unit, carriage and | Ball screw drive | |||
---|---|---|---|---|---|
Locating bearing | Non-locating bearing | ||||
d0 | P | ||||
mm | mm | ≈ g | |||
LTP15-185 | 20 | 5 | 2,6 | Lubricated | Lubricated |
10 | 3,1 | ||||
20 | 5 | ||||
50 | 10,6 | ||||
LTP15-275 | 20 | 5 | 2,6 | ||
10 | 3,1 | ||||
20 | 5 | ||||
50 | 10,6 | ||||
LTP25-325 | 32 | 5 | 5,4 | ||
10 | 7,1 | ||||
20 | 10,8 | ||||
40 | 13,5 | ||||
LTPG25-325 | 32 | 5 | 9,4 | ||
10 | 11,1 | ||||
20 | 14,8 | ||||
40 | 17,5 |
**If relubrication is required due to the application, please consult us.
Relubrication points
Relubrication can be carried out via a funnel type lubrication nipple in accordance with DIN 3405-A M8×1 on the side of the carriage unit, ➤ Figure. The thread of the lubrication nipple hole can also be used for connection to a central lubrication system. The carriage and the spindle nuts are supplied centrally with grease via this one lubrication nipple.
Lubrication points on linear table




Position of relubrication points
Designation | Mounting dimensions | |||||||||||
---|---|---|---|---|---|---|---|---|---|---|---|---|
Carriage unit | Locating bearing | Non-locating bearing | ||||||||||
|
| ⌀ |
|
|
| ⌀ |
|
|
| ⌀ |
| |
mm | mm | mm | mm | mm | mm | mm | mm | mm | mm | mm | mm | |
LTP15-185 | 11 | 74,5 | 15 | 5 | 26 | 6,5 | 15 | 3,5 | 10 | 14 | 15 | 3,5 |
LTP15-275 | 9,5 | 135 | ‒ | |||||||||
LTP25-325 | 10 | 150 | 26,5 | 17 |
**Countersink for lubrication nipple.
Lubrication points
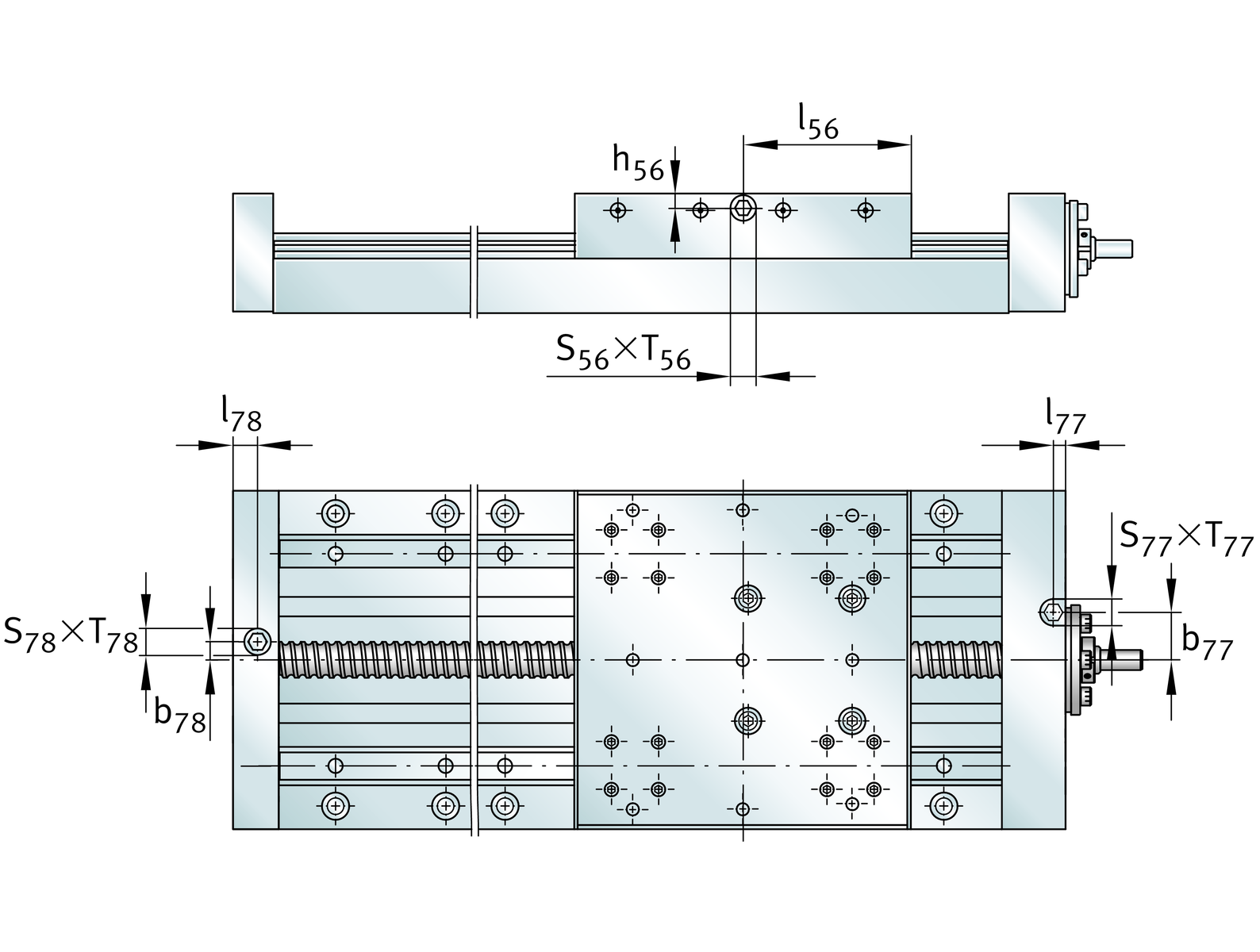
Lubrication nipples
High precision linear tables are lubricated via funnel type lubrication nipples NIP according to DIN 3405, ➤ Figure.
Funnel type lubrication nipple
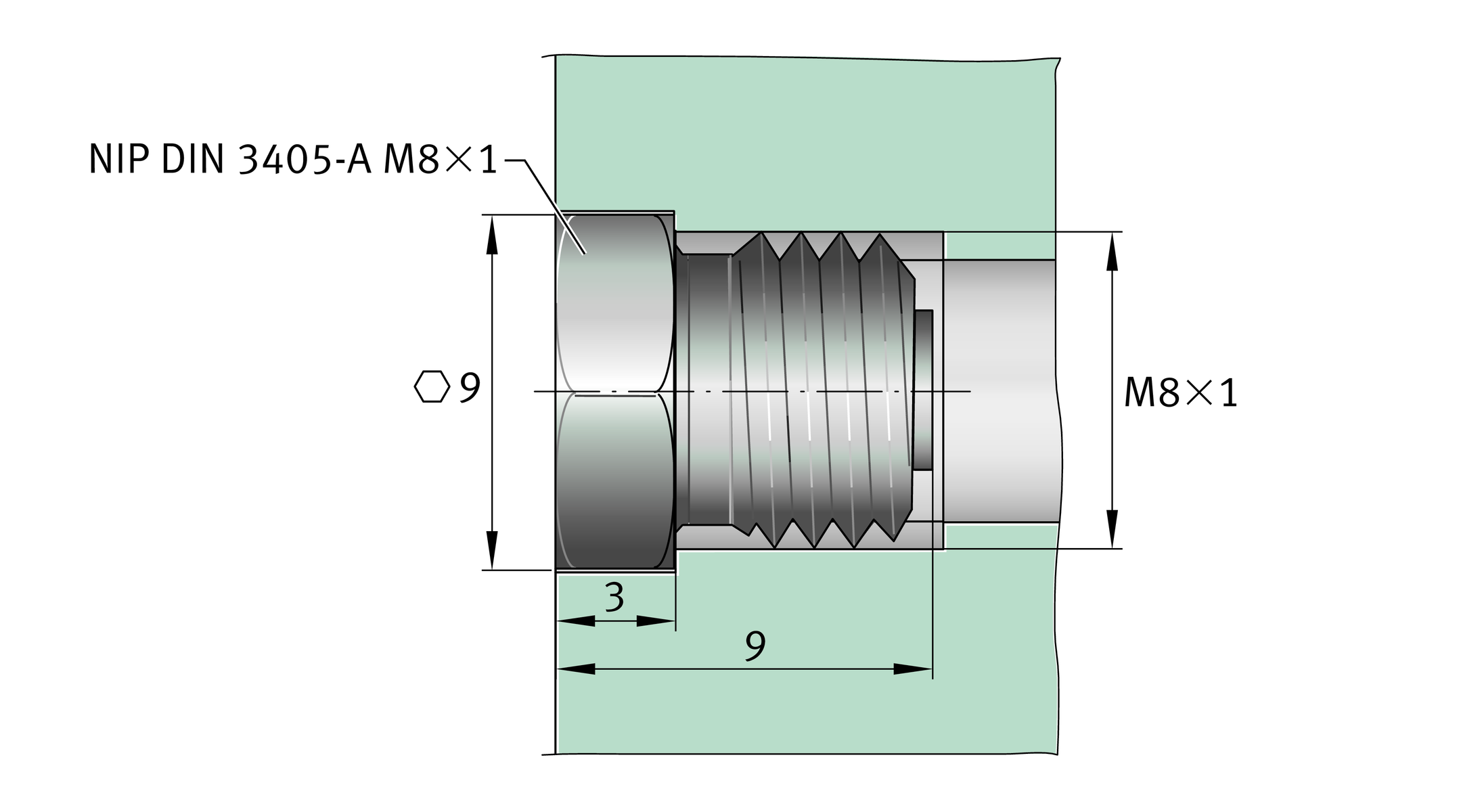
Maximum permissible spindle speed
Screw drives must not be allowed to run in the critical speed range.
The critical speed is essentially dependent on the following factors:
- spindle length
- spindle diameter
- spindle bearing arrangement
- mounting method.
The carriage unit velocity v is determined from the spindle speed n and the spindle pitch P. The limit values for velocities must be observed.
For calculation of the carriage unit velocity, the following applies: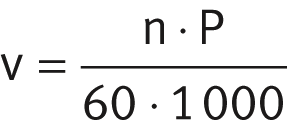
v | m/s | Carriage unit velocity |
n | min–1 | Spindle speed |
P | mm | Spindle pitch. |
Diagram
The diagram shows the relationship for individual series and sizes between the critical speed and the spindle length, ➤ Figure. The diagram takes account of the effective length BL of the bellows cover.
Maximum permissible spindle speed without spindle supports
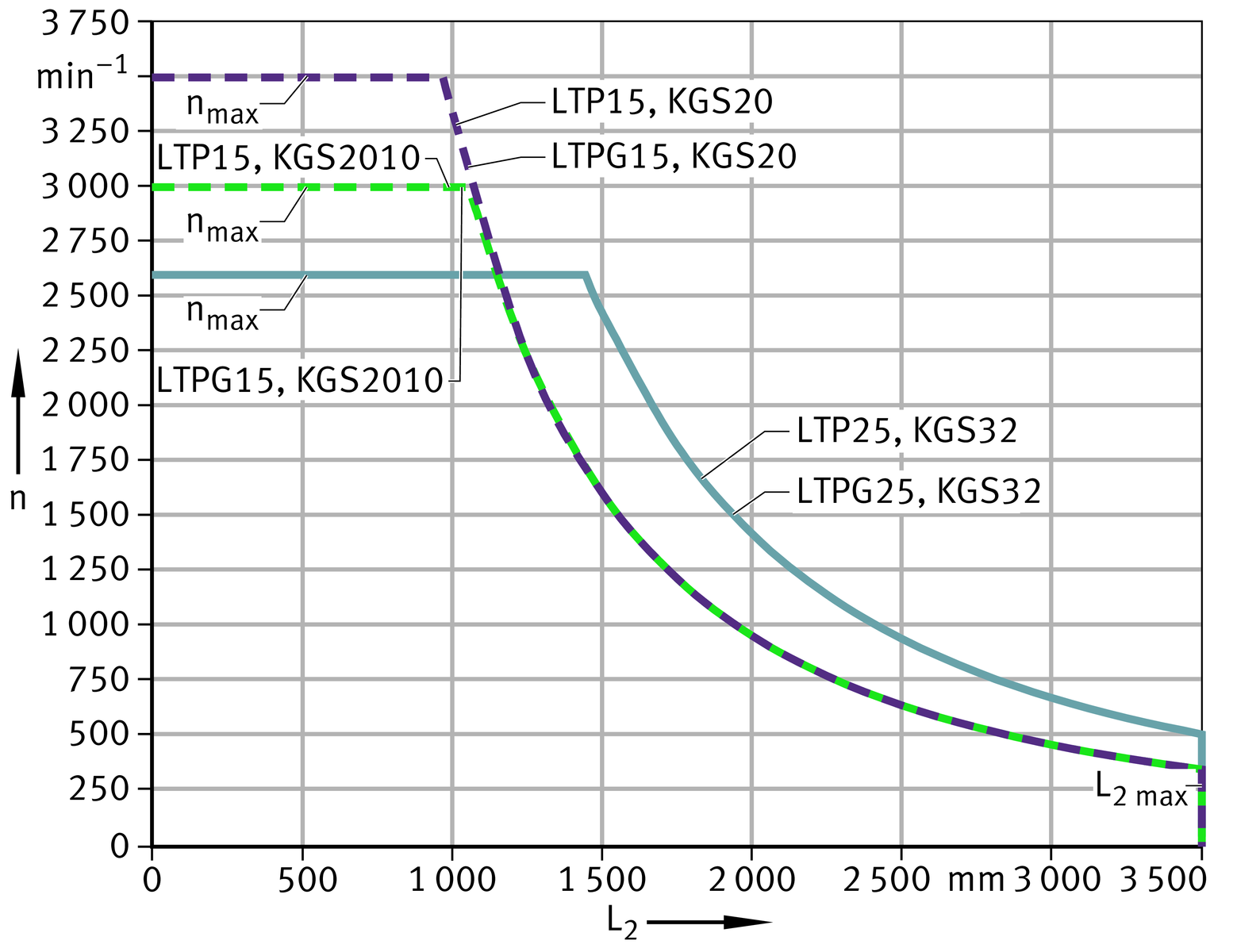
Kinematic operating limits
Maximum velocities are determined as a function of the critical spindle speed, see table. The limiting speed of the bearings can also restrict the spindle speed and thus the velocity.
Kinematic operating limits
Series and size | Spindle | Spindle nut design | Maximum acceleration a | Maximum velocity v | Maximum spindle speed n | ||
---|---|---|---|---|---|---|---|
d0 | P | ||||||
mm | mm | m/s2 | m/s | min–1 | |||
LTP15-185 | 20 | 5 | F | FM | 20 | 0,29 | 3 500** |
LTPG15-185 | 10 | F | FM | 0,5 | 3 000 | ||
LTP15-275 | 20 | F | ‒ | 1,16 | 3 500** | ||
LTPG15-275 | 50 | F | ‒ | 2,9 | 3 500** | ||
LTP25-325 | 32 | 5 | F | FM | 20 | 0,215 | 2 600** |
LTPG25-325 | 10 | F | FM | 0,43 | 2 600** | ||
20 | F | FM | 0,86 | 2 600** | |||
40 | F | ‒ | 1,73 | 2 600** |
**Restricted by the limiting speed of the bearing with grease lubrication.
Mounting requirements
The information on the influences of the adjacent construction of LTP matches the information on the influences of the adjacent construction of LTE. The information on the mounting position and mounting arrangement of LTP matches the information on the mounting position and mounting arrangement of LTE. The only information covered here is that which is additional to or different from the information given previously.
Location
If the geometrical characteristics of high precision linear tables LTP and LTPG are to be fully utilised, mounting on completely flat supporting surfaces with low roughness values is necessary. Linear tables LTP and LTPG are located on the adjacent construction via the base plate by means of conventional screws. The components to be moved are also located on the carriage unit by means of conventional screws.
For location of the linear tables, all the fixing holes should be used.
ATTENTION
If the total length is small, not all the fixing holes in the base plate may be accessible. In such cases, please consult the Schaeffler engineering service.
Location of the high precision linear table
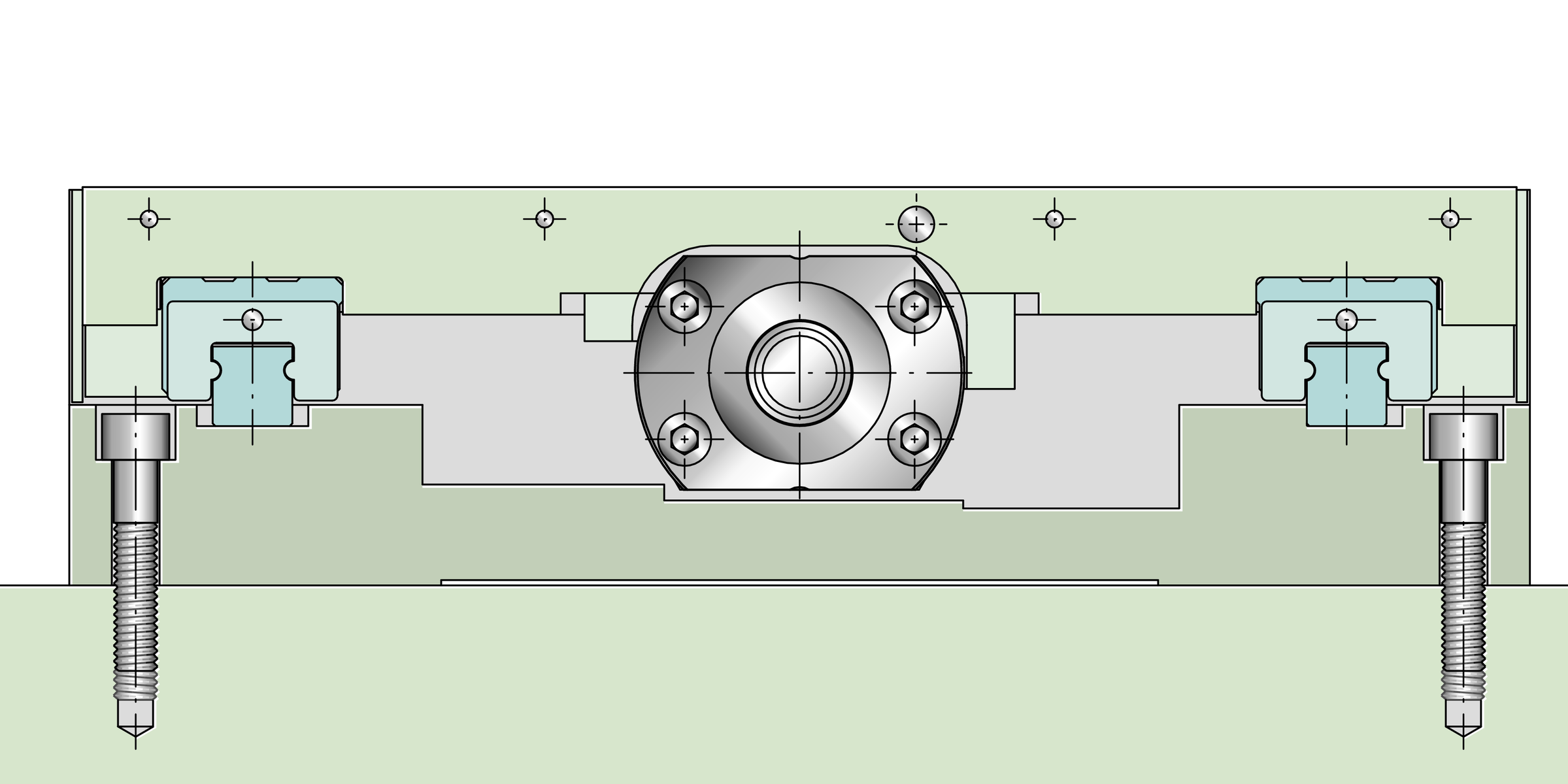
Accuracy
Length tolerances
Length tolerances of high precision linear tables LTP and LTPG, ➤ Figure and table.
Length tolerances
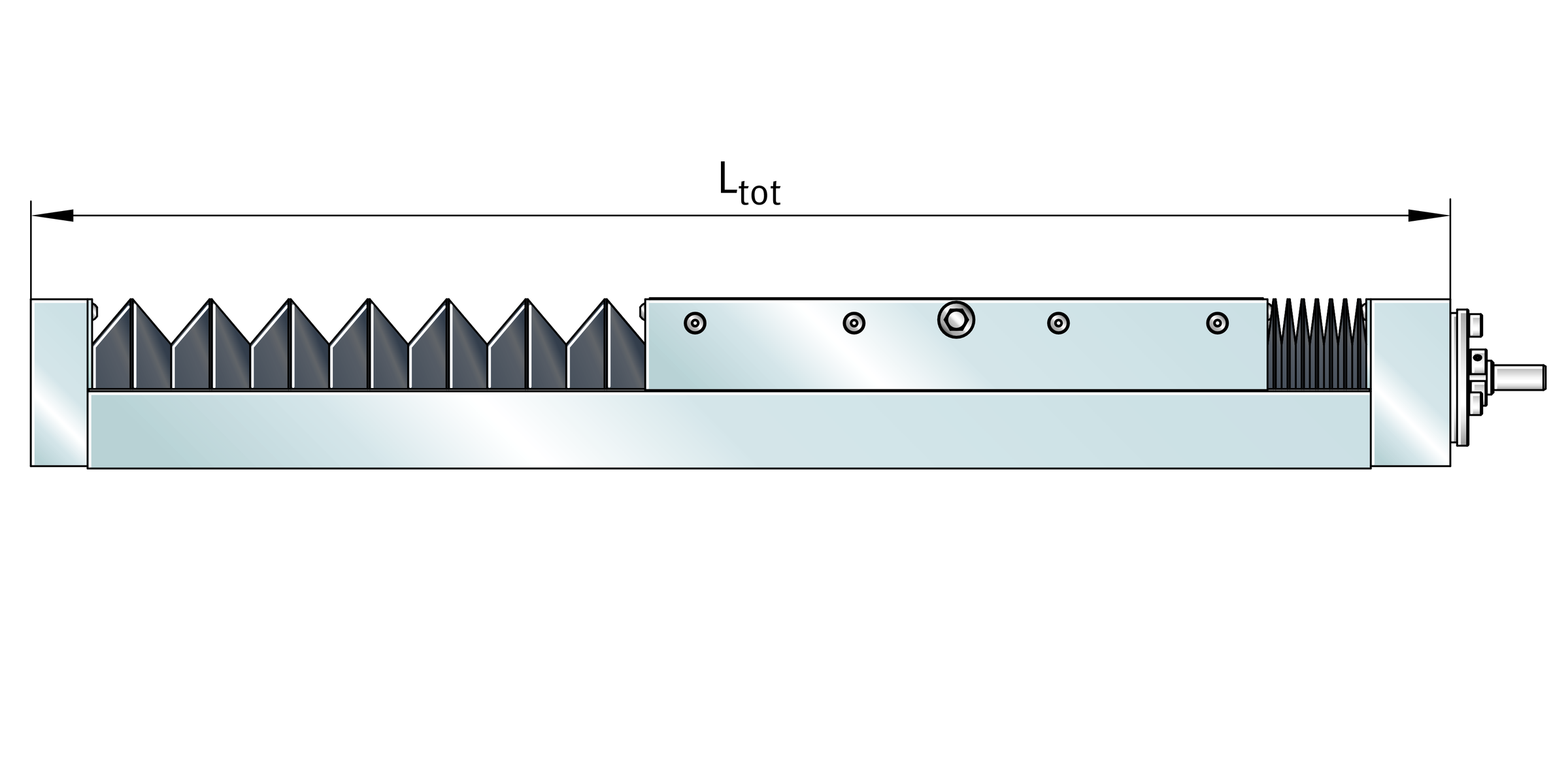
Tolerances
Total length Ltot | Tolerance | |
---|---|---|
mm | mm | |
Ltot ≦ | 3 500 | –1 |
Pitch accuracy of spindle
High precision linear tables with ball screw drive are available with a single flanged nut with clearance, see table. Where higher accuracy requirements are present, preloaded (clearance-free) double nuts are possible for many pitch values, see table.
ATTENTION
In the case of high precision linear tables, the nut unit (double nut) can only be preloaded clearance-free if the spindle pitch P is less than the nominal diameter d0 of the spindle.
Ball screw drive
Series and size | Spindle | Spindle nut | ||||
---|---|---|---|---|---|---|
⌀ d0 | P | Pitch accuracy
| Single or double nut | Suffix | Axial clearance | |
P | max. | |||||
mm | mm | μm each 300 mm | mm | |||
LTP15-185 LTPG15-185 | 20 | 5 | 50 | Single | F | 0,05 |
Double | FM | Preloaded | ||||
10 | Single | F | 0,05 | |||
Double | FM | Preloaded | ||||
20 | Single | F | 0,05 | |||
50 | ||||||
LTP15-275 LTPG15-275 | 5 | Single | F | 0,05 | ||
Double | FM | Preloaded | ||||
10 | Single | F | 0,05 | |||
Double | FM | Preloaded | ||||
20 | Single | F | 0,05 | |||
50 | ||||||
LTP25-325 LTPG25-325 | 32 | 5 | Single | F | 0,05 | |
Double | FM | Preloaded | ||||
10 | Single | F | 0,05 | |||
Double | FM | Preloaded | ||||
20 | Single | F | 0,05 | |||
Double | FM | Preloaded | ||||
40 | Single | F | 0,05 |
Parallelism values
The parallelism values T1 and T2 are based on an ideally flat locating surface. Geometrical deviations of the locating surface are not taken into consideration.
The values in the diagrams are standard accuracies, ➤ Figure and ➤ Figure.
During measurement of the values, the following conditions apply:
- T1 and T2 measured with a clamped base plate, where all fixing holes must be used
- parallelism in a longitudinal direction measured at the centre of the carriage unit.
Parallelism and straightness
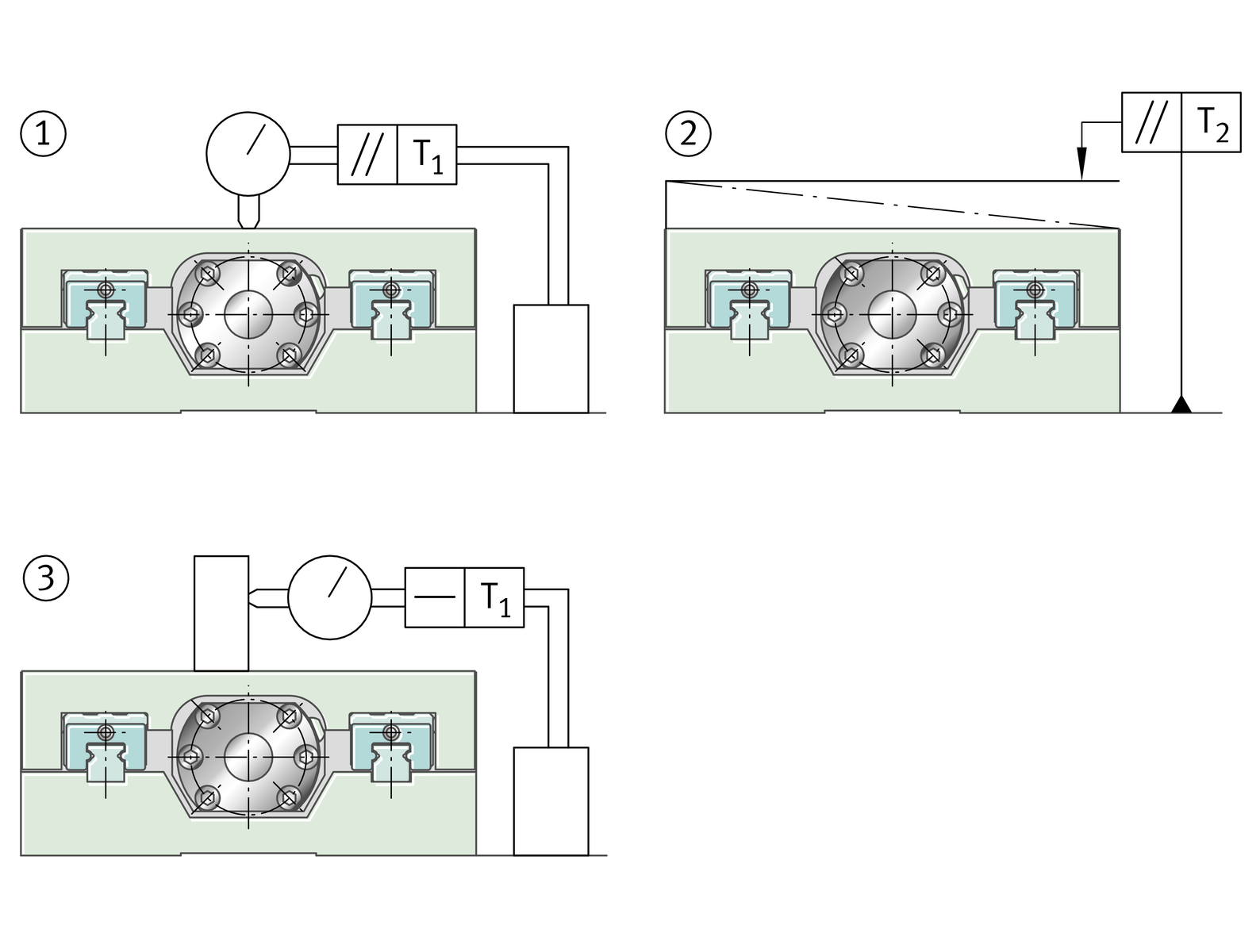



Accuracy values
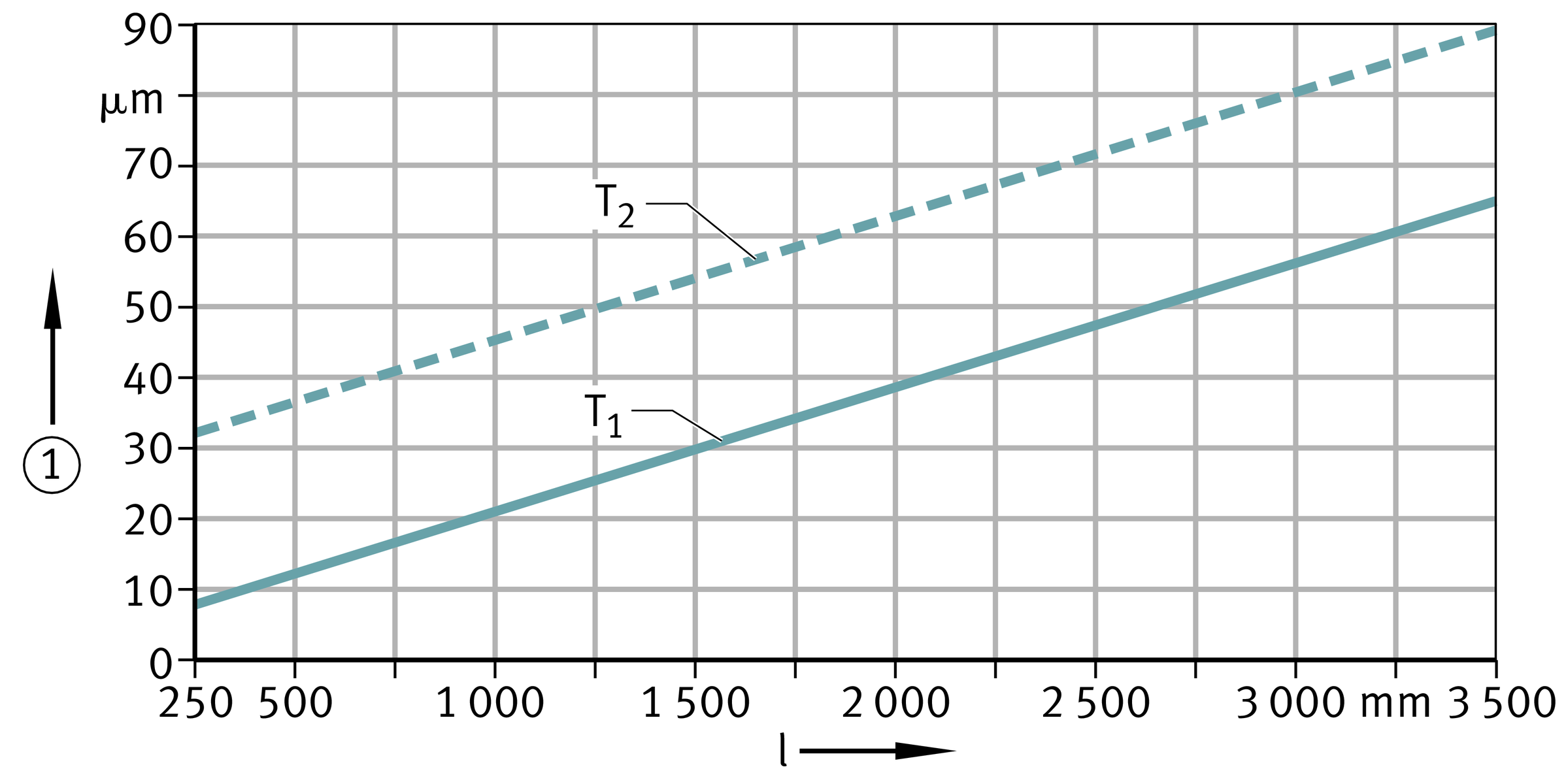

Accuracy values
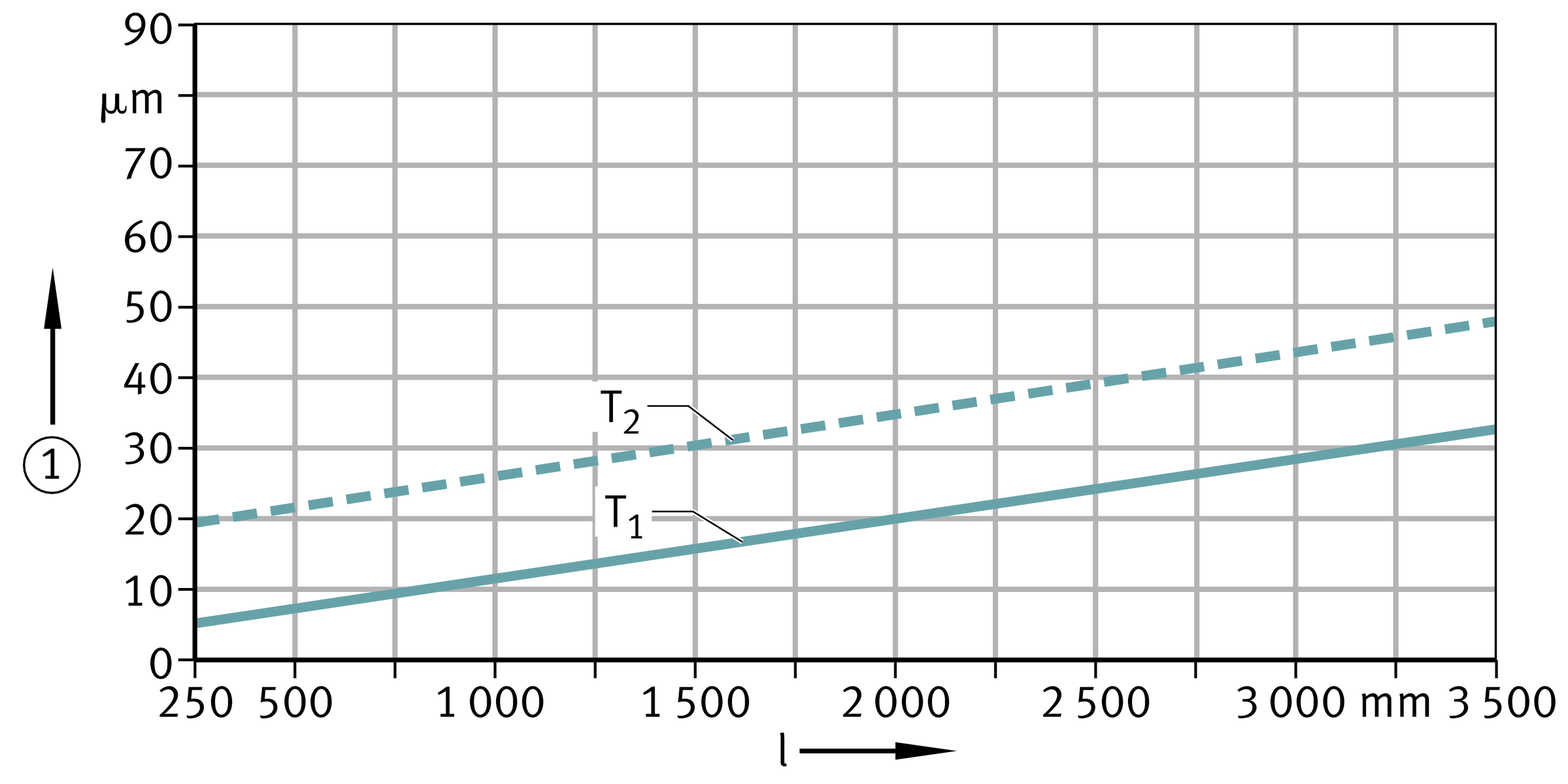
